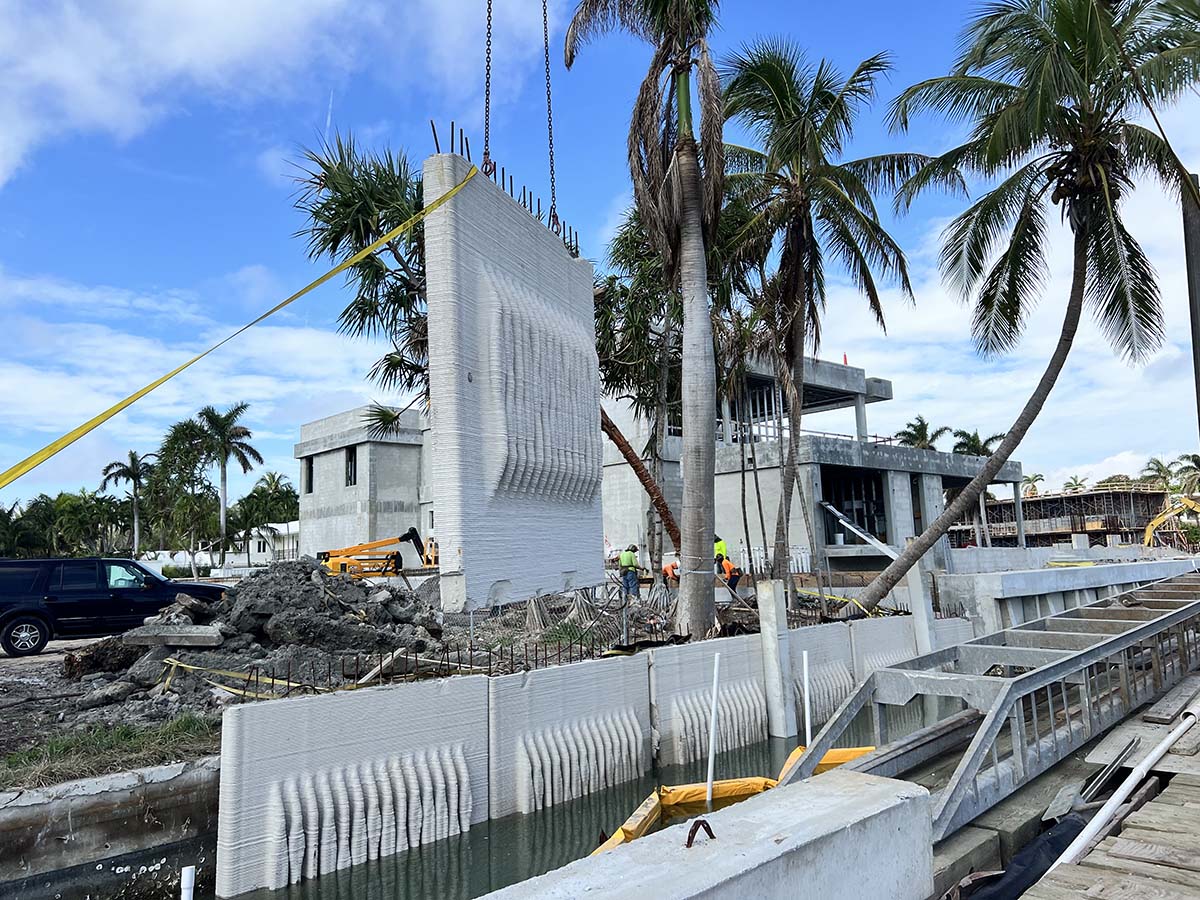
3D Printed Seawalls: Eco-Friendly Erosion Control
Published on May 2, 2024Merging structural necessity with environmental correctness is at minimum a challenge and at worst impossible. Manmade construction will always impact nature that was here first. However, the consciousness of finding common ground has grown, as have solutions. The world’s first 3D-printed Living Seawalls™️, by Kind Designs, is a perfect solution, as it aims to protect shorelines while creating habitat.
The idea for Living Seawalls was sparked by CEO Anya Freeman back when she was running her own law firm in South Beach. “I noticed we had worse and worse flooding each year. One year my roommates and I got a letter from our car insurance carrier that flooding would no longer be covered. That was a big problem. There was so much doom and gloom conversation, but no one was talking about solutions and using technology,” she said. She put a team together and they came up with the idea that printing seawalls would be a cheaper and potentially better solution to keep water back and prevent erosion.
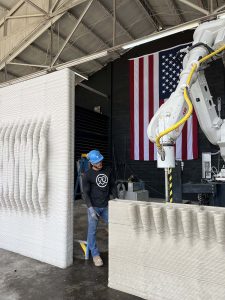
That idea led to the company Kind Designs and the creation of Living Seawalls. The company, its operations and production, are based in Miami, Florida, in a 50,000-square-foot facility on the Miami River. The waterfront location allows the company to transport the panels they construct by barge. Unlike some conventional manufacturing, here three robots do the heavy work.
Printing a Seawall
Traditional seawalls are made by pouring concrete into molds that contractors make or buy and then letting the concrete set, generally over about three weeks.
Living Seawalls start with printed hollow mortar filled out with a rebar cage and then filled with specially formulated 5000 PSI concrete that is environmentally friendly. Mixing the concrete used in conventional seawalls requires high temperatures, and the concrete often has chloride, metals or other toxins as a part of the mixture. The high temperature requires high energy, and the components of the concrete can be environmentally harmful when used in fragile marine ecosystems.
The proprietary mix of Living Seawalls has no toxins and is pH neutral. It has been used in artificial reefs and drinking water reservoirs for many years, so it has historical data to back up its safety. To continue building on the data, Kind Designs builds water quality sensors directly into its walls to collect water quality information in real time. An added eco-friendly advantage of Living Seawalls over traditional is that the mixing process is done at a 30% lower temperature so the carbon footprint of creating the seawalls is less than that of traditional walls.
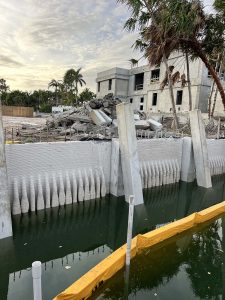
The strength of the wall comes from rebar, as it does in traditional concrete seawalls. The spacing of the rebar throughout the wall determines how strong it will be. The closer together the rebar, the stronger the wall. However, Freeman said that while rebar is still used in the 3D printed walls, she and her team are researching alternatives to the metal. “Rebar eventually rusts and that’s what makes walls fail. The rebar expands and pops the concrete, so the lifespan is generally no more than 50 years. We already have a way to reinforce our panels without rebar, we’re just waiting for approval from building codes. Romans didn’t use rebar in their seawalls and those are still standing today. We hope to have a product that lasts 500 years,” Freeman said.
Kind Designs has an exclusive agreement with Netherlands-based Cybe for the supply of the fastest robot arms on the market. The robots can print at 500mm per second with a small resolution size. A 10 x 10-foot panel can be printed in less than an hour.
A Green Choice
The layers in a Living Seawall are just a half-inch thick which enables more creativity in the design and gives the walls 60% more surface area than concrete walls. Where seawalls have received negative attention for the disruption they can cause to habitats, and the shifts in sands they can cause as they reflect waves, Living Seawalls are designed to be a positive for the environment. The walls are created to mimic natural habitats with pockets and crevices for marine life to hide and a surface that allows organisms to attach.
Kind Design’s first installation, a 100-foot seawall for a private residence in Miami, was constructed to mimic a mangrove that would be naturally found in this area.
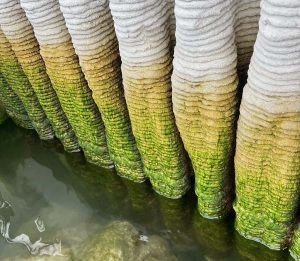
In addition, the Living Seawalls absorb wave action because the surface is not flat. Conventional seawalls are flat, and waves bounce off them, causing a change in littoral current that can shift sand flow, causing unwanted shoaling or erosion. The impacts on currents and sands from a Living Seawall are greatly reduced.
For contractors, the benefit of Living Seawalls is how quickly they can be printed and delivered, and the reduced production cost. Once a project is permitted, the seawalls can be ready within 30 days, which is up to 90 times faster than the lead time on concrete. The Kind Designs team reviews permitted plans and then customizes the slabs to meet the specs of the project.
Looking ahead, Freeman wants to see a tax incentive for the use of Living Seawalls similar to what’s given for carbon-reducing products like solar panels or electric cars. “I’d like to see a green premium and expedited permitting for Living Seawalls. We are in the category of living shorelines, and we are the only one in the United States to offer gray/green infrastructure,” she said.
Gray/green infrastructure is something the U.S. Army Corps of Engineers is researching and looking to adopt. Green infrastructure is completely natural, like planting native grasses, but can be impractical or impossible for many applications and locations. Gray infrastructure is something like conventional concrete walls that use toxic materials and can harm habitat. Gray/Green combines environmentally friendly with practical and durable solutions. “We’d like to see our walls mandated because they reduce the carbon footprint, have no added costs and attract organisms,” Freeman said.
For now, the team at Kind Designs will wait to see if the USACE approves of the use of Living Seawalls as a gray/green solution, and in the meantime keep rolling out their product for private and public shorelines across the United States and looking for more ways to use 3D printing as an eco-friendly solution.
To see a video of the construction process, click here.
Categories | |
Tags |