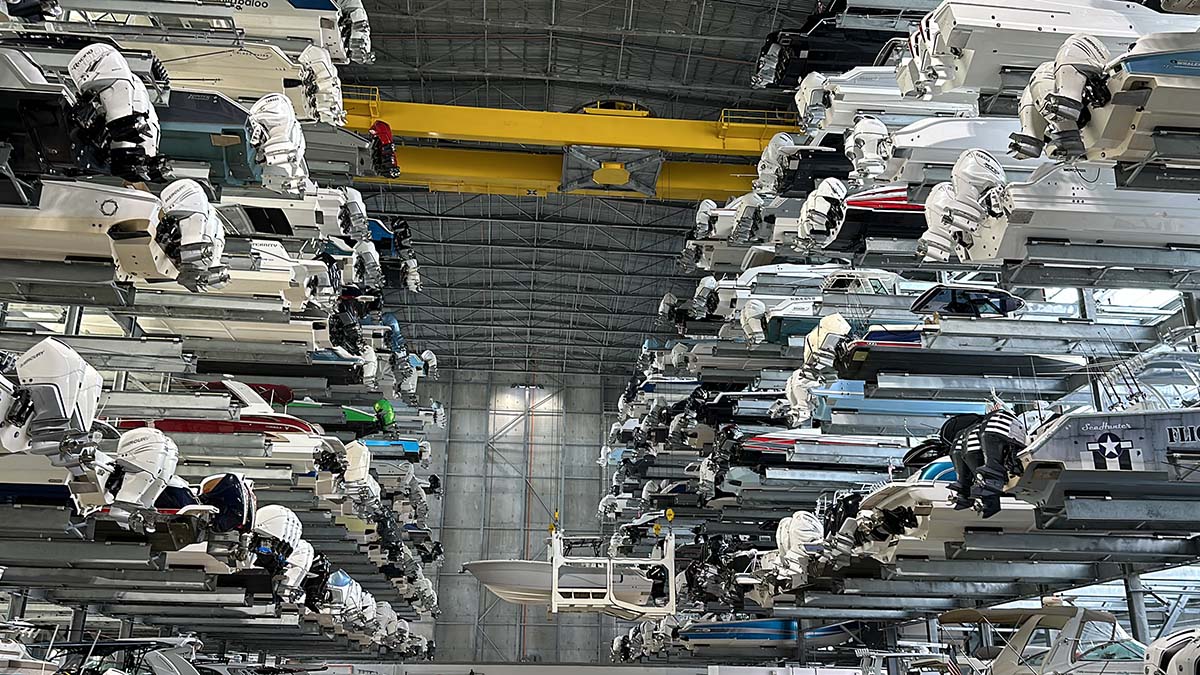
Cranes, Automation and Electrification of Dry Stack Marinas
Published on November 4, 2024As dry stack marinas continue to grow in popularity with boaters, the technologies supporting dry stack facilities continue to evolve and improve. We are all familiar with traditional facilities that use forklifts to move boats from the racks to the water, and this approach is tried and tested. But is it the best approach for all sites? Or are there good reasons to consider an alternative approach?
Alternatives
The alternatives to the traditional forklift approach include systems that utilize electromechanical components such as cranes and derivatives of automated parking systems of various types to move boats from the rack to the water, each with advantages and disadvantages.
Overhead Bridge Crane: An overhead bridge crane relies on a girder system that rolls back and forth on a fixed frame of permanent runway beams and support columns, usually fully integrated into the building structure. Integration of the crane into the building structure can increase the cost of the building as more weight is carried at the top of the building. The overhead bridge crane lifts boats off the rack using a cradle, usually suspended from cables; however, a column and fork system is also possible.
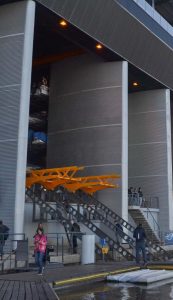
Ground-Mounted Cranes: A ground-mounted crane is composed of a girder system rolling on tracks mounted on the ground. A rotating vertical column is mounted to the girder system, and movable forks are mounted to the column. Since the whole system is mounted to the ground, the building structure does not have to carry the weight of the crane and is therefore potentially less expensive. Maintenance of a ground-mounted crane is easier, since all of the motors and moving parts are accessible from the ground.
Logistics Equipment Derivatives: These are storage solutions adapted to move boats in enclosed environments. Since they come from logistics warehouses for industrial and commercial solutions, these trans-elevators are tested worldwide and on a considerable variety of cargo. One example of this is Gulf Star Marina in Fort Myers, Florida, which is powered by ASAR equipment from Austria.
Automated Parking Derivatives: These systems are based on car parking, mainly in large urban environments. They require a re-design of the traditional racking system to accommodate the different elevators and the horizontal transport mechanisms. They rely on a series of movable cradles and sensors to store boats.
Multi-stage Systems: A multi-stage system uses one of the electro-mechanical systems to remove the boat from the rack and move it to a separate system that launches the boat into the water. Known as launchers or coastal elevators, these separate systems improve the efficiency of the crane by allowing boats to be launched and retrieved separately on the elevators and then placed in the rack by the crane. Coastal elevators also offer two critical advantages, which are impossible with forklift systems. First, they can accommodate a huge range in water levels simply by lengthening the launch rails to almost any vertical distance needed. Second, they can be mounted at the second level, allowing the boats to be launched over a public walkway on the waterfront. Also, the coastal elevators prevent the water from the forks (in traditional forklift facilities) from getting into the warehousing area, reducing corrosion risk, especially in saltwater environments.
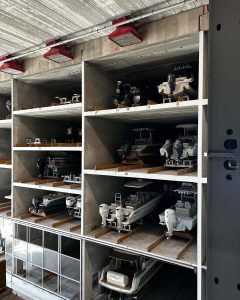
Automated or Human Operated?
Regardless of which crane system is used, they can be either manually directed by a human operator or fully automated using computer systems, lasers or LiDAR systems to guide them while supervised by a human operator.
The fully automated systems offer the advantage of the most accurate movement of the boat with the lowest likelihood of damage. While no system is perfect, automated systems have many fail safes built in, along with a manual override, that stops the system in the event of a fault and allows manual operation until the problem is solved. Human error is essentially eliminated from the equation, and operators of automated systems report less damage to boats. The cost of a fully automated system is higher, but that cost is made up in efficiency and less damage.
Some operators are more comfortable with a human operator directing the crane, and this approach is less expensive than a fully automated system. Human error is more likely, but partially automated systems can incorporate fail safes to assist the human operator.
Comparing the Systems
The perceived advantages of the traditional forklift operation include lower upfront costs for the rack system, reliability of modern forklifts and simply the comfort of continuing with a familiar approach that has worked well for a long time. There are downsides to this traditional approach that the developer of a dry stack facility needs to consider, including the noise and exhaust of internal combustion engines that can be an issue with neighbors and regulators, who might also be concerned about engine fluids leaking into the water. Tire dust is also an issue for boat owners and operators who struggle to keep vessels and facilities clean. We are very excited to see more and more electric powered forklifts, such as the Wiggins eBull, which is fully electric, quieter and requires less maintenance than traditional internal combustion power train equipment.
Other issues are less obvious until you consider them directly in comparison with the advantages of a system that utilizes a crane rather than a forklift. The
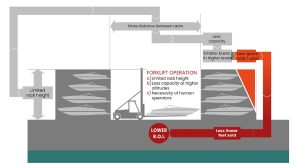
biggest loss of revenue for the dry stack operator caused by the forklift system is the fact that the forklift cannot lift a larger, heavier (more profitable) boat on the higher racks due to the limitations of the forklift. Since the boats the forklift can lift get smaller and smaller the higher the rack, there is a triangular void space where no revenue is generated, as seen in Figure 1.
A crane system, however, has no similar limitation, and it can lift the same size and weight boat to any available rack, no matter the height. This maximizes the developer’s revenue and therefore the return on investment.
The spatial efficiency advantages of crane systems go farther in two very important ways. First, the electro-mechanical systems can lift boats much higher than a forklift, so more boats can be stored on the same area of land. Second, the aisle space between the racks can be narrower with an electro-mechanical system than what is required for maneuvering a forklift, either reducing the overall footprint of the building or allowing the storage of larger
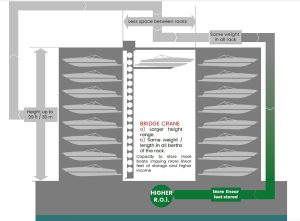
boats in the same footprint, as seen in Figure 2. With land costs being such a large part of the equation in densely populated areas, building higher and narrower can mean the difference between a financially viable dry stack marina and one that can’t be financed.
Maintenance Requirements
But what about maintenance? What happens if the crane breaks down? It is important to remember that all systems require maintenance, and anything mechanical can break down (including forklifts). That said, it is much easier to have a second forklift on hand than a second crane. For that reason, maintenance of the crane systems is paramount. Fortunately, the crane systems in question have been in use moving steel and heavy equipment for far longer than we have been moving boats with forklifts, and there are many more crane systems in use around the clock than will ever be used to move boats. All these crane systems in factories are similarly critical to the operation of the facility, and therefore a system of preventative maintenance to keep them running around the clock is in place and very well understood. There are very few moving parts, and replacement parts can be kept on hand for an emergency repair.
In Conclusion
There is no single right answer for all dry stack operations, and it is important to consider your alternatives. If your facility is located in a remote area with a lot of land, then it may be easiest to take the traditional forklift or one of the cost-effective crane system approaches. On the other hand, if you want to build a high-end facility in the heart of Fort Lauderdale, an automated rack system might be your best choice, or even your only choice.
F3 Marina Fort Lauderdale is a new fully automated facility that opened in 2023 and has set a new global standard for dry stack marinas. This facility can hold 240 boats up to 43 feet in length, 13-foot beam, 17-foot height, and up to 30,000 pounds, stored in a hurricane-rated building in racks six levels high.
Located just off the 17th Street Causeway in Fort Lauderdale, F3 Marina Fort Lauderdale offers unsurpassed amenities, first-class service and convenient access to numerous restaurants, hotels, shops, local activities and more. The marina has direct access to the Intracoastal Waterway and is just minutes from the Atlantic Ocean.
Located on a parcel of just 1.5 acres in size, on some of the most desirable waterfront property in Florida, the spatial efficiency of the facility and density of boats allowed by the height of the structure were the only way to build a financially viable facility. The architecture of the facility fits in beautifully with the neighborhood, with extensive use of windows, green walls and a building shape specifically designed to minimize shadows being cast on neighboring residential properties.
The use of the bridge crane allows for the ground floor to be used for on-site parking and the marina offices and lounge, without compromising boat storage capacity above. Without the ability to park under the boats, zoning approval would have been much more difficult to achieve.
In summary, new technologies for moving and storing boats are opening up more sites for the development of higher density, more profitable dry stack marinas.
Categories | |
Tags |