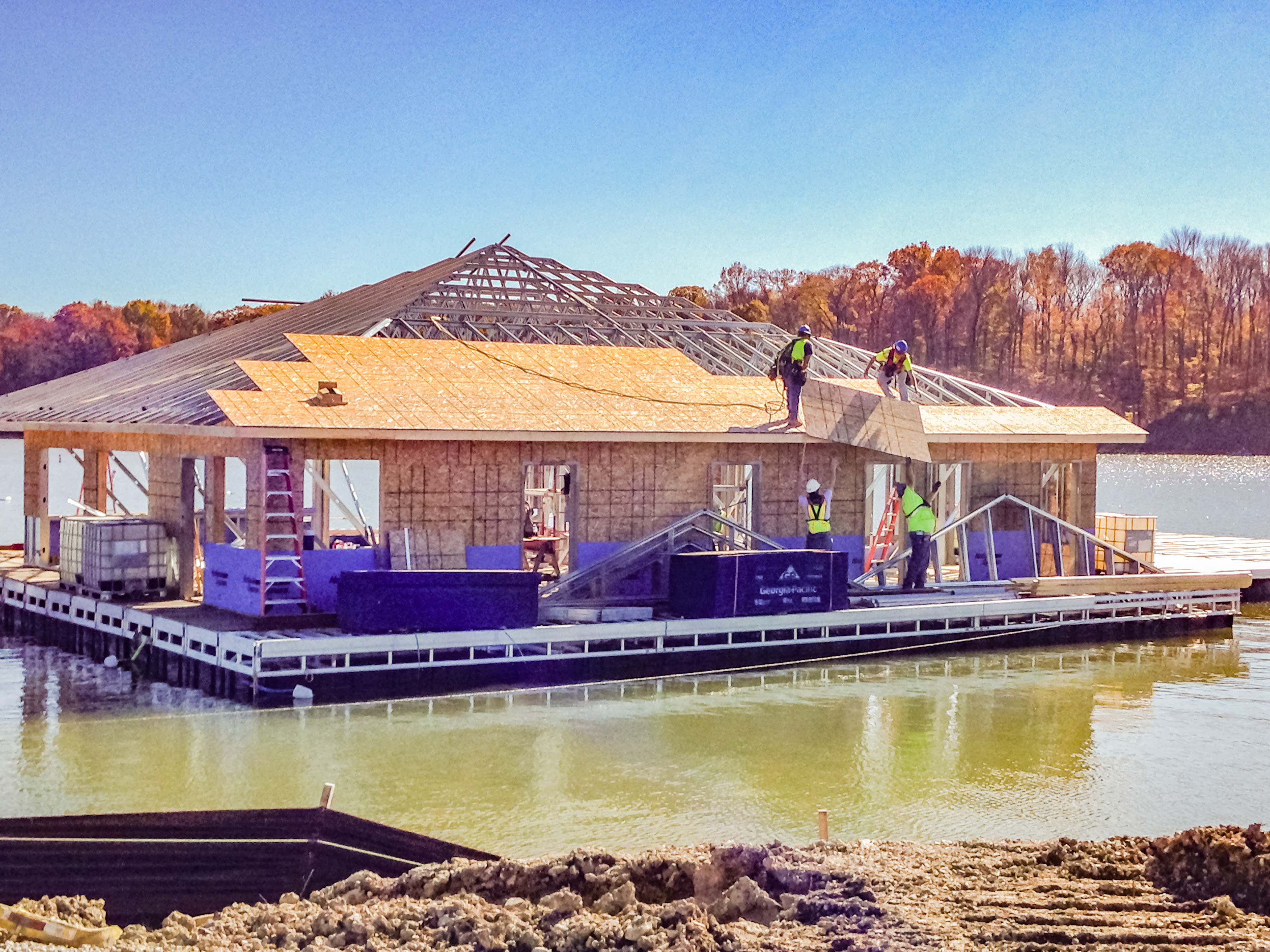
Laying the Foundations for Floating Marina Architecture
Published on February 14, 2019Floating building infrastructure is a growing trend in marina design and construction. The reasons for this vary but are frequently due to a lack of upland area for additional facilities, or the desire to locate marina amenities closer to the end users. In areas that are experiencing an increase in coastal or overland flooding, floating architecture also provides an effective resilient strategy to keep buildings and services out of harm’s way.
Whatever the reason, the construction of new floating facilities is ultimately driven by the key role these structures play as revenue generators and marketing assets for the marina. The most common floating building uses include restrooms, laundry, marina services/stores and rental offices, fueling, restaurants, and outdoor bar areas. The correct design is a critical element for long-term operational success.
To rest a building’s foundation on the water, unique considerations need to be taken into account at every step of the process. From initial programming and planning all the way through structural design, materials selection and construction, marina owners, their design/engineering teams, and the dock manufacturers must work closely together in order to deliver a successful project that functions as intended.
Programming and Planning
Prior to having the platform constructed, the programming for a floating building should consider both immediate and future/potential customer and operational needs. What starts out as a floating marina services building with restrooms and laundry, or a restaurant/snack bar with marina offices and storage, could potentially shift down the road. The decisions made during this initial programming stage greatly impact the capacity of the floating platform to accommodate desired uses. Without careful consideration and coordination, difficulties may arise both during construction and in future use of the facility.
Working with the owner/operator, the architectural/engineering (A/E) team can help determine the current and future needs of both the marina operator and users. The A/E then evaluates this programming information, in conjunction with the dock manufacturer to quantify the weight loads and structural requirements posed by projected uses. This process informs the proper base on which to build the facility. If the owner, A/E, or manufacturer work in a vacuum during any point of the process, missteps are likely to limit the kind of programming and use the base dock/platform can support.
Considerations for building design during the programming phase should include:
Access
• An accessible route to the building is required to meet ADA and building/zoning code requirements.
• The access route must also be suitable for deliveries and garbage removal.
Fire Protection
• Determine what level of fire protection and firefighter access will be required.
• Meet with the local approval authority to discuss early on in the project.
Location
• Will the building location provide acceptable proximity and offer value to patrons?
• Will anticipated low water levels support the installation without grounding?
• If the building will be allowed to ground, does the design provide an acceptable level of protection to prevent damage to the floatation system?
• Will marina dredging or other maintenance needs require the building be able to be repositioned in order to complete the work?
• Does the marina basin have an acceptable wave climate for structural longevity of the floating building, or will additional wave mitigation be required?
• Can the building be anchored with an existing dock system or will it require its own anchoring? This is an important consideration, given that the building will have a greater wind profile and loading requirements than the dock system it may be connected to.
Design and Materials Selection
As weight is a major factor in both the structural and flotation design of the substructure, steel framing should be considered in place of standard wood-framed building construction. Special care should be taken concerning the methodology of waterproofing the area between the floor and dock surface, as well as insulating the area between the floor of the building and the dock.
Considerations for HVAC and sanitary sewage pumping are also extremely important. The utility area required for the MEP systems may be larger than expected due to the complexity required for the plumbing. The high in/out traffic of patrons accessing a marina services building offering food/beverage requires different insulation methods for HVAC ducting in humid climates to prevent condensation.
Floating platforms for the building can be of two main types: rigid or semi-rigid. Both have pros and cons associated with their use that present their own particular challenges for the building designer and contractor.
Rigid floating platforms are mainly constructed of concrete pontoons. The pontoons are normally precast offsite and delivered to the project site, placed in the water, and fastened together through mechanical connections, whalers or post-tensioned cables. These rigid platforms normally have a wooden foundation that rests on top of the concrete platform. The building materials used on rigid platforms can also be more rigid (e.g., stone veneer, exterior insulation finishing systems (EIFS), and drywall), since there is less likelihood of long-term development of flexural cracks. Normally the concrete base is relatively flat and level to the water surface, making it an easier substrate on which to construct the building. Planning for sanitary drainage facilities on rigid platforms must be coordinated with the dock manufacturer to allow for the cutouts and chases necessary to install piping and pumping systems.
Semi-rigid floating platforms are normally constructed of truss-based, floating docks sections with either floatation tubs (polyethylene encased expanded polystyrene tubs) or metal pontoon/floats underneath. The benefits of using a truss-based system are directly related to the ease of transport to the site, the familiarity dock manufacturers have with these systems, and the ease of routing of utilities through the substructure of the docks (especially drainage piping for sanitary services).
To keep the semi-rigid dock structure level once the building is in use, it is common to provide differing depths of floatation tubs in specific areas based upon the anticipated loads applied by the building and its various uses. This buoyancy distribution can present assembly issues as well as construction complications. Ballasting of the structure will be required during construction of the building, so that weight distribution can be adjusted as needed. Building interior finishes will benefit from the use of less rigid panels, such as fiberglass-reinforced plastic, in lieu of standard drywall, ceramic/stone tiles or other rigid finishes that are more prone to crack when the platforms shift.
Flooring choices should lean toward resilient sheet goods or engineered wood products that are suitable for wet locations.
Loading and Leveling
While the loading demands posed by building uses have a direct impact on the design and stability of the floating structure, the A/E must also work with the dock manufacturer to satisfy a wider range of regulatory requirements. A floating building platform must be designed for uniform live (moving) and dead (fixed/stationary) loads in a manner that will meet the requirements of building codes and space use categories, such as the International Building Code (IBC). In addition to addressing load-bearing walls and column loads from the building structure, there are other specific items that should be shared with the manufacturer in order to more fully understand how the overall structural system will ultimately react to such loads.
The following items may exceed the code-based designated live and dead loads that a floating building may experience, requiring special consideration during the design process:
• Bait tanks
• Battery sales and storage
• Refrigeration and freezer space
• Beverage storage
• Vending machines
• Packaged ice coolers
• Fryers and other heavy cooking appliances
• Number of patrons visiting a restaurant/bar or attending a special event
These added loads need to be carefully evaluated with the platform manufacturer to determine how they will impact the placement of floatation or ballast. Depending on the type of floating platform (such as concrete pontoon, dock with floatation tubs, or custom floatation and ballasts), different depths of floatation units may be required in order to properly level the structure once its fully loaded.
As mentioned earlier, these leveling issues can pose additional challenges during and after construction of the dock platform. The first challenge will be the potential for each dock section to float at differing levels prior to the building loads being applied. Once the platform is fully assembled, the dock surface is still unlikely to present a level surface for the structure to be built. This will make it difficult for the contractor to build walls.
To overcome this obstacle, temporary ballasts will need to be placed on the dock surface in order to “pre-load” the dock and create a levelled building surface. As different building sections are built, the ballast can be adjusted. On-deck bulk storage of building materials also affects the floatation of the platform structure, requiring additional leveling adjustments as construction progresses.
Floating buildings offer great opportunity and value for both marina operators and patrons. Realizing that value requires a highly informed, collaborative design and construction process to ensure a solid foundation for building program and performance.
Robert Wright is a senior civil and waterfront engineer with SmithGroup. He can be contacted at 608-327-4433 or at Robert.Wright@smithgroup.com
Categories | |
Tags |