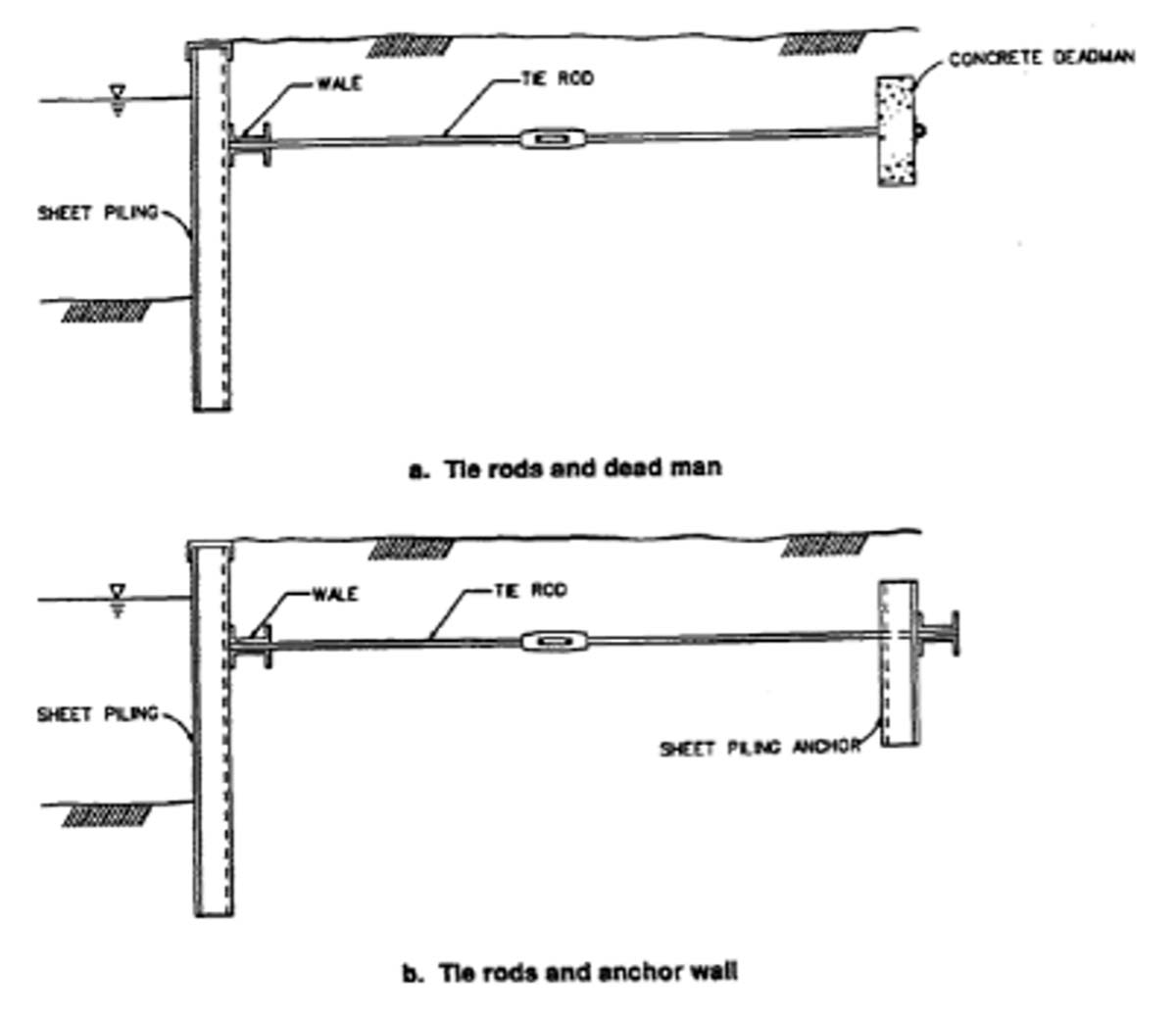
What is Geotechnical Engineering and How Does it Relate to Marinas?
Published on August 23, 2022“What’s the dirt like” …probably the most derogatory question that could be posed to a geotechnical engineer. Geotechnical engineers work with soil, not dirt. A concept my University of Wisconsin – Madison Professor Dante Fratta drilled (pun fully intended) into all of his soil mechanics students. Soil is made up of specifically defined constituents like clay, silt, sand, and gravel which can be studied, researched, and modeled for various engineering applications. Dirt is just the stuff dogs roll around in. Simply stated, geotechnical engineers apply physics and engineering principles to all structures that interact with the soil. Marinas and other waterfront infrastructure are no exception.
Geotechnical engineering can be especially challenging in these environments since the soils may be many feet underwater, so you have no clue as to what you might be dealing with.
How is Soil Defined?
A little more detail on how to define soils is required before diving deeper into how geotechnical engineering is applied to marina structures. There are several standardized ways to describe the mechanical and physical properties of soil. But for the purposes of this article and for non-engineers working around marinas, soils can be broadly put into two different categories: coarse-grained and fine -grained soils.
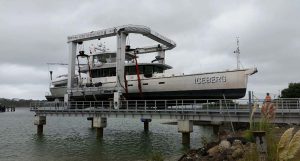
Coarse-grained soils include sand-sized particles (0.06 mm to 2.0 mm) and anything larger in diameter. On the small side of that range, if you can see individual grains with your eyes, you are dealing with sand. Anything greater than that can include rip rap used to line drainage ditches, rounded “river rock”, and larger 15-ton (6.5 feet in diameter) armor stones used for breakwaters. Though their size varies dramatically, they all behave mechanically the same. The majority of their engineering properties are driven by gravity and interlocking with other particles.
Fine-grained materials, such as silt and clay, behave much differently and are not as affected by gravity. The grains are so small that forces between the grains are stronger than the force of gravity. When handling clay, this phenomenon manifests itself with the clay feeling “sticky”. This is also the reason why fine-grained material can be shaped and molded for pottery applications. The same cannot be said with sand. Additionally, fine-grained material compresses much differently than coarse-grained material. They can be squeezed and compacted to a much higher degree than sand and gravel can be. You can get a sense of this by thinking about handling sand (coarse-grained) or clay (fine-grained) with your hands. At the beach when making a sandcastle, once you fill the mold with sand, you cannot compact the material in there much. Once you fill the mold, that’s it. But that is not the case with clay. Clay can be placed loosely in the mold or can be compacted in lifts to add much more material than just in the loosest state.
The type of soil that makes up a particular site is difficult to predict and therefore good information is needed when designing different marina components.
Piles and Bulkheads
Two of the more common and basic pieces of marina infrastructure are piles and bulkheads. Piles are long, skinny structural members used to transfer load from the water surface (or above the water surface) down to soils strong enough to handle that load. A common example is a foundation support for a structure. A load at the top of the pile pushes down along the length of the pile and the soils at the bottom of the pile, sometimes referred to as the pile toe, are strong enough to resist that load. Especially in marine or lake environments, the top layer of soils are soft or weak and piles can be used to reach stronger soils, or even rock below. Buildings, piers, decks, and boardwalks are all types of structures that can be supported on piles.
Figure 1 is an example of a travel lift pier. The weight of the crane, weight of the boat, and weight of the decks are all supported by the six steel piles. Those piles transfer that load to a strong soil layer (sometimes a rock layer) below so that when the load is at its maximum with the boat hanging in the air, the pier does not settle or move vertically at all. One can imagine that even tiny amounts of vertical movement can cause cracking or failures in structures.
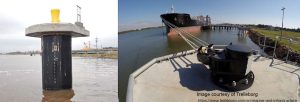
Another extremely common application of piles is for anchorage. Marinas with floating docks need to keep all those boats in the same location. This can also be achieved with piles embedded into the subsurface. Occasionally, individual piles are used to keep one large vessel in place (Figure 2). The piles are working against wind and wave loads being applied to the docks or the vessel itself. In these types of scenarios, the load is pushing on the side of the pile, not vertically like before, and causes bending in the pile. Like before with vertical loads, the piles need to be embedded deep enough so there is enough strength in the soil to resist the load being applied to the side of the pile.
Figure 3 shows a pile used to anchor docks that have suffered lateral loading over a long period of time and can be observed by the fact that the pile is no longer straight. Over the years, it has fatigued and permanently deflected from the force the boats and docks are imparting on the pile. Oh yes, fatigue, that is how something breaks over the years because of repeated loading, pushing, and pulling back. In some cases, the pile itself does not actually deform, but the pile has cycled the soils around it, sort of pushing it incrementally past its lateral strength until the soil around the piles has deformed and compressed.
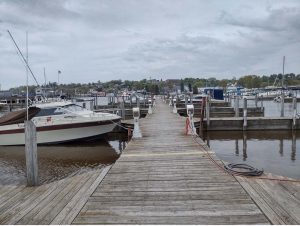
A bulkhead is a catch-all term for any type of retaining wall at the waterfront. The retaining wall can be made from a poured concrete wall, wood piles, steel sheet piles, poly-vinyl sheets, or pre-cast concrete blocks that stack on top of each other. The objective is normally to create a wall so that vessels can tie up along its edge. In some cases, deep drafted commercial vessels require walls that extend upwards 20 feet or more from the water’s surface. In other cases, extreme tides may expose 30 feet of wall daily.
Walls can be built cantilevered or tied back. Cantilever walls are basically just a row of piles lined up, one next to the other. This method has limitations in terms of how tall it can be built, as the pressure from soil placed behind the wall quickly exceeds the bending resistance of the wall. This causes it to lean, or more likely, break. Therefore, in nearly all situations, the wall retaining all that soil needs to be anchored with what is commonly referred to as a “dead man” or an anchorage system. The anchorage system is commonly made up of large blocks of poured concrete, piles embedded to a sufficient depth, or another row of sheets. These anchors are all then tied to the main retaining wall to resist movement. The dead man and steel sheet pile anchoring system are demonstrated schematically in Figure 4.
So why are these structures made of steel and concrete being designed by engineers that work with soil? It’s the same reason why foundations are designed by geotechnical engineers. The foundation intimately interacts with the soil and the soil is being considered just as much in the design as is the concrete or steel members. Piles are used to extend to a more competent soil layer. So, understanding the strength of the soil is critical to estimating how long piles need to be. Soils also have a degree of internal strength. Weaker soils will impart more load on a retaining wall, necessitating a stronger wall and a larger anchorage system. The strength of the soils also will affect how far the anchorage system needs to be in relation to the main wall.
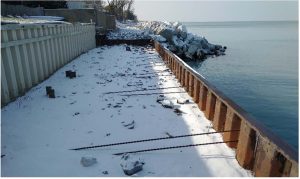
The difference in the soil behavior of coarse- and fine-grained material also affects the design and construction. Normally piles are driven to their required depth with a large hammer. However, a layer of large boulders could make this type of construction more difficult and expensive by getting in the way of the advancing pile. Clays have the capacity to compress and squeeze under a load and it is key to understanding how much it will compress under the design load. Excessive settlement and consolidation can lead to cracking and decreased functionality over time. Also, much like basement walls, engineers need to prevent water from building up behind these walls. That extra water adds significant pressure applied horizontally to the wall. Using more coarse-grained material will allow that water to dissipate and leave the system since fine-grained material “absorbs” and holds water much more. Depending on the material, the walls need to have “weep” holes or paths for that water to escape. Understanding the project site’s soils and design loads is critical to a cost-effective structure that performs well over its design life.
Geotechnical Reports and Subsurface Investigations
Geotechnical reports or subsurface investigations are used to obtain project specific soils information needed to complete the design of piles and bulkheads. This involves coordinating drill rigs that advance a probe, hammer that probe into the soil layer at a specific energy, retrieve the soil sample, and then classify the soil sample by its constituents and resistance to that hammering. Without this data, more assumptions need to be made about the soils leading to more conservativism in the design which is typically reflected in higher construction and material costs. An appropriate investigation includes an adequate number of borings in the approximate location of the proposed structure. Soils are extremely heterogenous and can vary wildly over short distances. As an owner or operator of a marina or waterfront facility, it is important to keep that in mind. Just because a certain pile or wall design works at one spot, 50 feet away it could be totally different, so it is important to seek the guidance of a geotechnical engineer to make that judgment and interpretation.
As it relates to the subsurface and geotechnical reports, consider the following:
The subsurface does not change as fast as human development. Meaning, that an old report used for a different structure may contain useful information for a future design or redevelopment. Drilling three offshore borings 20 feet below the surface will typically cost about $30,000 after mobilizing a barge and drill crew. With other saved data sources, future costs to get geotechnical data may be avoided.
Geotechnical reports are used to mitigate risk in the subsurface for a proposed structure. When buying an old house, it’s difficult to imagine proceeding without thorough inspections to ensure the structure and mechanical components are commensurate to what is the expected value. Otherwise, you could find yourself with some expensive and unanticipated short-term costs. It is no different with anchoring docks, building retaining walls, and developing a waterfront site.
Geotechnical engineering is sometimes referred to as the “invisible” side of civil engineering because you rarely see the major components while walking around a project site. Additionally, people rarely think about how the soils affect the design of infrastructure and tend to focus on the concrete, steel, or more architectural parts. However, soils serve as the literal foundation for everything humans build. Marinas, waterfronts, and coastal developments are no different.
Nick Stefani, PE is a project engineer with Edgewater Resources. He can be reached at nstefani@edgewaterresources.com
Categories | |
Tags |