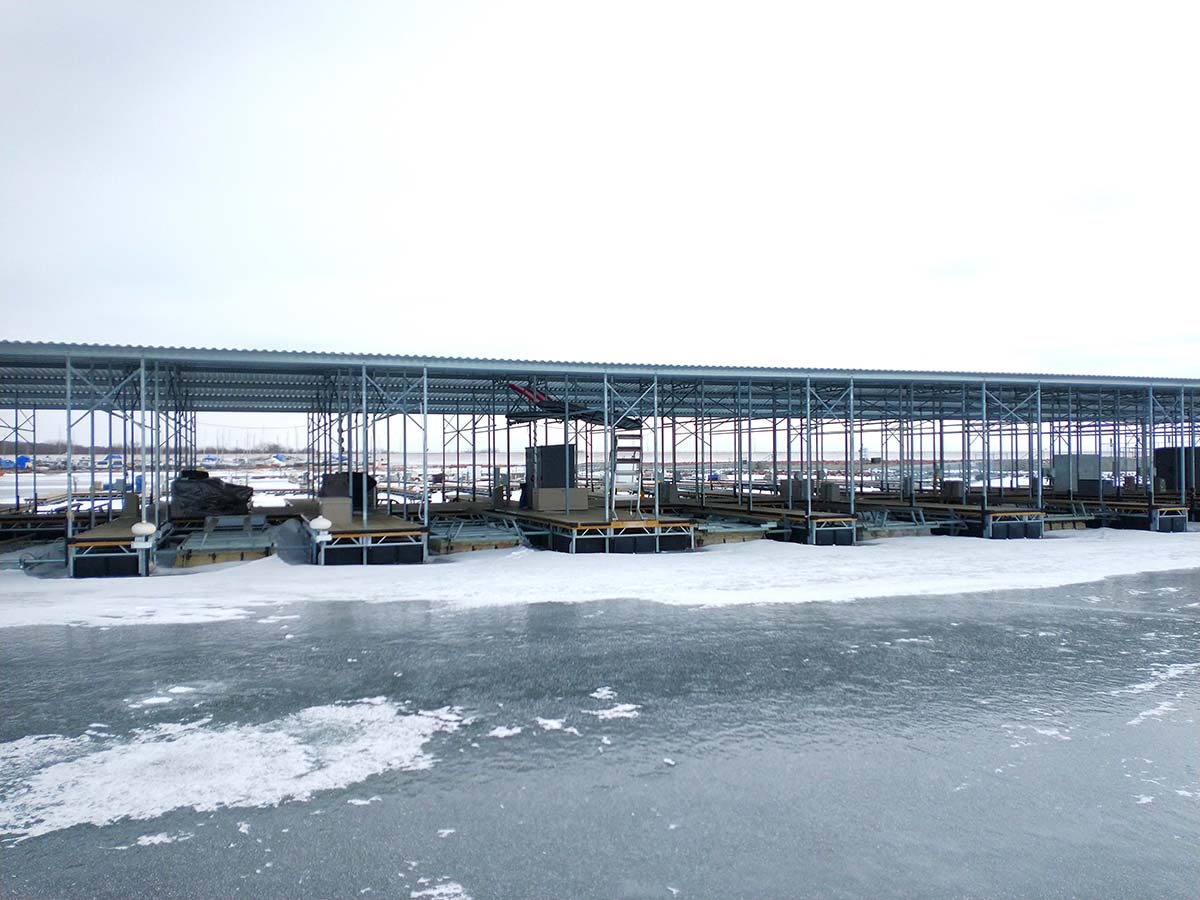
Winter Happens: Are You Ready for What it May Deliver?
Published on August 15, 2024Winter comes in all shapes and sizes — from the plummeting temperatures and extreme events of the north to the dramatic freeze-thaw cycles of our central states. For many marinas, this means damage. Heaving shorelines, damaged docks, contorted piles and support systems can be recurring and costly problems if left unaddressed. Yet winter can also be unpredictable, making it difficult for marinas to calculate the risks or appropriate protective measures to put in place.
Conducting a Site Evaluation
Because marinas are unique ecosystems, each has different environmental inputs, historic weather patterns, predominant winds and ice impacts. Evaluating and understanding these local conditions allows an engineer to formulate the best possible solutions to protect against ice damage.
A proper site evaluation will consider many factors: overall site topography and slope; historic ice thickness; bathymetric conditions; wave, wind and ice loads; composition of marina infrastructure; and the level of protection needed to successfully mitigate winter environments.
Assessing Site Topography and Slope
Topography and slope are important factors at marinas located on lakes or rivers that freeze. Ice heave occurs when sheets of ice expand or are blown by wind against the slope of a shoreline. This effectively pushes back the shoreline and can bulldoze undersized or poorly engineered revetment stones into the landscape. Ice heave can also “pluck” or displace revetment stones entirely.
When properly designed and constructed, stone revetments dissipate wave and ice energy before it can cause erosion or damage. Consisting of an armor layer, a filter layer and toe protection, these systems can be very effective in absorbing extreme weather inputs while protecting underlying material and structures from erosion and scour. The size of revetment stones required depends on the slope of the land above and below the waterline. Shallower slopes have lower run-ups and are less prone to ice heave, so smaller stones will generally suffice. Steep slopes, however, will require larger stones for protection. A simple application of dumping random-sized rip rap will not do the trick.
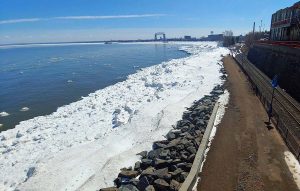
This is where engaging a coastal engineer and implementing engineered solutions is critical. A professional engineer will calculate the required median size of armor stone by diameter and weight to withstand waves, wind and ice forces at that specific location. The engineer will also calculate the true design ice thickness number for the site, which requires a thorough analysis of current and historic ice thickness data collected from varying locations to inform the design parameters for the project.
Reviewing Bathymetric Conditions
A bathymetric survey collects data such as the depth, topography, activity and features of underwater terrain — the lake, river or sea floor. The survey can be conducted in a few ways but is generally done by a person on a boat with an echo sounder that sends an array of beams across the floor of the water body to collect data. It can also be conducted using Light Detection and Ranging (LiDAR) in some environments — a remote sensing technology that uses light in the form of a laser to transmit a pulse into the water and employs the data from the return signal to create a map. Bathymetric surveys help engineers understand the underwater environment and identify early any potential hazards or risks.
Determining Wave, Wind and Ice Loads
Waves and water carry a great deal of energy, which doesn’t simply disappear when covered with a layer of ice. In fact, the force of wind and waves can place immense pressure on ice, causing it to heave and shove against shorelines and create damage. Another challenge in designing for cold climates is the movement of ice due to expansion and contraction. This, too, can generate a great deal of pressure. When ice heats up during the day, cracks develop and fill up with water — which later freeze and expand — contributing additional pressure to any marina infrastructure the ice encounters during these cycles.
One of the best ways to understand potential wave, wind and ice contributions on a given body of water is to generate a digital model of the site. Inputs such as average wind speed, direction and return rate — as well as wave generation, transformation and breaking rate — can be used to simulate a storm event and surge scenarios, which can influence how protective revetment structures are designed.
Considering Protective Measures
Many marinas located in winter-impacted geographies already have protective measures in place. Stone revetments, breakwaters, sea walls, vertical sheet walls and chain and anchor systems can all do a great job of fortifying marina basins.
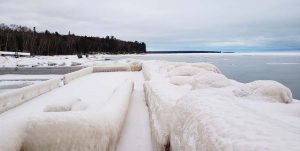
But what about the contents within? Docks, floats, boats, gangways, storage areas, covered structures and support systems are all at risk of damage from ice forces and winter conditions.
In many instances, floating docks can be disconnected, left in place and allowed to “ride” a minimal amount of ice cover while still anchored within a general vicinity. This can be a worthwhile option because the docks don’t risk freezing together due to excessive restraint and potentially breaking apart in spring when elements thaw at different rates. This method also minimizes yearly costs of maintenance and spring set-up time.
If marinas opt to keep the entire dock system intact throughout the winter, floats must be engineered with extra buoyancy, so their movement doesn’t destroy finger piers or other supportive infrastructure under heavy ice loads. Even if the water body itself doesn’t amass a substantial amount of sheet ice, a marina might still experience atmospheric icing and snow cover that accumulates on the tops of docks. This weight can cause docks to sink, infrastructure and dock frames to bend and twist and floats to crack, which can render marinas unsafe or non-compliant with Americans with Disabilities Act (ADA) standards.
Low-floating or sinking docks mean that the floats are no longer working properly. Newer docks, if designed correctly, will have more freeboard and can be found practically on top of the ice when winter arrives, which keeps all metal and steel components nicely above water and ice levels.
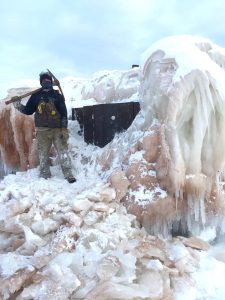
Damaged and sinking floats mean the dock steel frames are pushed deeper in the water. The lower the dock structure, the more ice that adheres to the floats and frames. A marina might have success in implementing bubblers or water circulators within their dock systems to keep ice thin and to prevent it from building up on dock float and frame surfaces, but not all winter conditions are created equal, and it is not always the right solution for every situation.
Similarly, boat storage areas or structures with covered roofs should be mindful of ice loads — particularly if they are metal and left intact year-round. Many climates don’t receive snow in winter yet can receive several inches of ice instead. The immense weight applied to otherwise skeletal infrastructure can wreak havoc. Metal roofs also get cold quickly, so any level of humidity or added moisture in the air can build up — in the form of ice.
Appraising Existing Conditions and Next Steps
Due to these potentially harsh winter inputs and damaging impacts, marinas need to take an honest assessment of the age and condition of their infrastructure and conduct a cost-versus-risk analysis to determine when upgrades are necessary. Left unaddressed, damaged floats, dock infrastructure and shorelines might need repair annually, which is an escalating and recurring expense. At some point, the yearly fix-it fund becomes unsustainable. Choosing to invest in new or upgraded infrastructure before it reaches the point of no return will save marinas time, money, potential insurance rate hikes and headaches.
Dan Williams, PLA, ASLA, AHLP is senior landscape architect at MSA. He can be reached at dwilliams@msa-ps.com. Zac Morris, PE is coastal engineer/department manager at AMI Consulting Engineers. He can be reached at zac.morris@amiengineers.com. Marcus Rue, PE is project manager at MSA. He can be reached at mrue@msa-ps.com.
Categories | |
Tags |